What is Shock Testing?
March 20, 2020
Back to: Shock Testing
Systems in industries like defense and electronics must properly function after a shock event in the field. Shock tests typically involve a sharp transfer of energy into a mechanical system to test its capability to survive a drop, hit, impact, fall, explosion, or other source of transient vibration. These events include package drops, vehicle impacts, electronic mishandling, and a variety of other bumps, slams, and falls.
Shock Pulses
Test specifications like MIL-STD-810, IEC 60068, or RTCA DO-160 include shock testing for product qualification or to confirm durability/reliability. The specifications define the shock pulse parameters and classify the pulse as a classical shock or transient waveform that represent a real-world event.
Shock pulses can range in time duration from a few milliseconds to upwards of one minute. many Many test specifications define classical shock pulses in terms of acceleration, but assess the severity based on the resulting change in velocity (ΔV).
Why ΔV?
Structural damage is more often correlated with a change in velocity than peak acceleration. ΔV represents the total shock imparted to a system, while acceleration indicates how quickly that shock occurred.
Failure modes such as cracks, fractures, or displacement relate to the total impulse, not just how quickly it occurred. High acceleration over a short time may not transfer much energy, but a large ΔV can induce significant structural stress.
Classifications of Shock Pulses
Classical Shock Pulses
Classical shock pulses are the simplest method of generating a shock pulse. They have a pre-defined shape, amplitude, direction, and duration. The library of basic pulse shapes derives from historical drop test data. Examples of classical pulse shapes include half-sine, initial-peak, terminal-peak, square, triangle, sawtooth, trapezoid, and haversine.
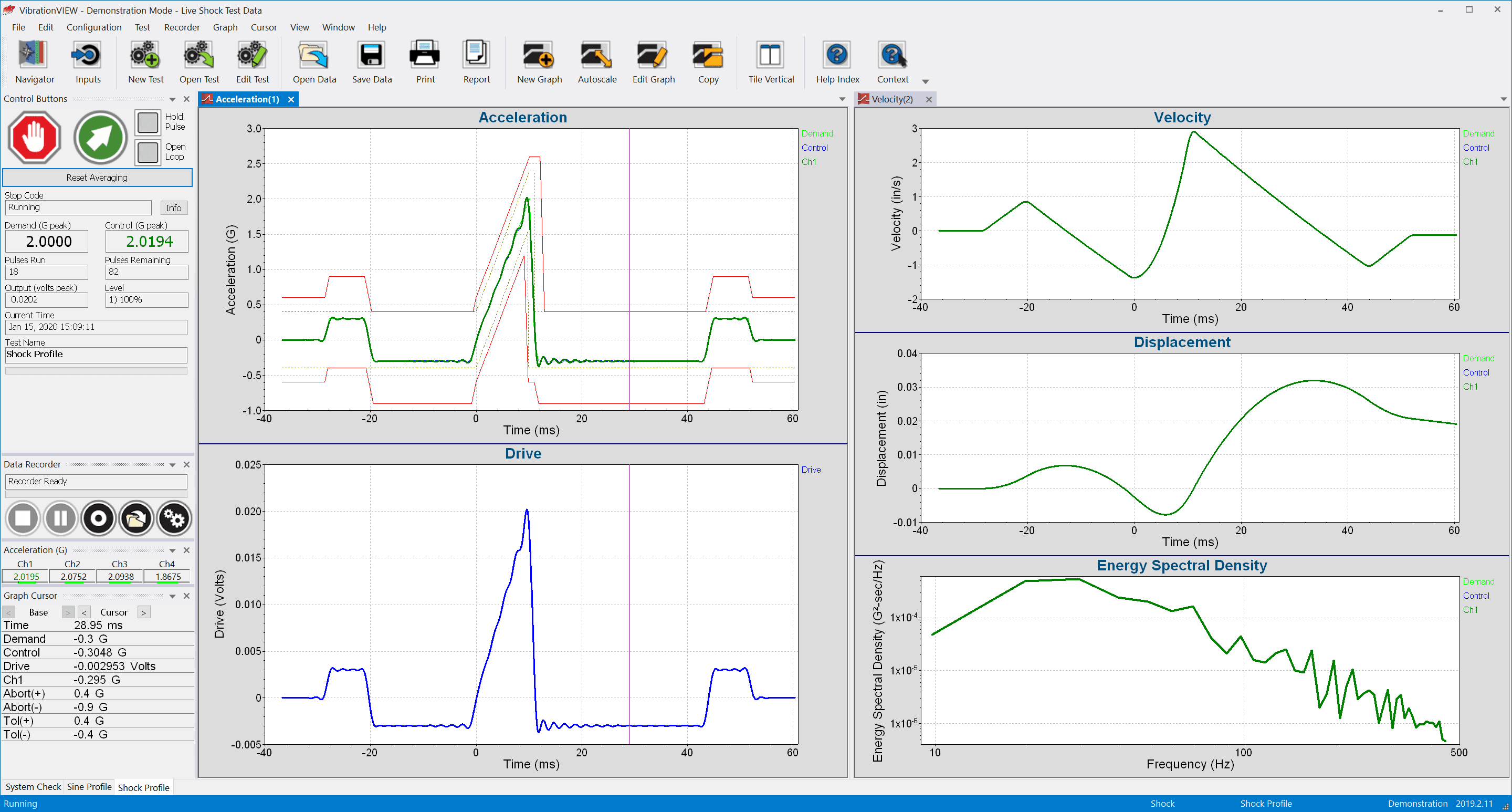
Classical shock pulse in VibrationVIEW.
Drop tests were designed to generate a unipolar acceleration shape with a set ΔV. The acceleration shapes have carried over to shaker testing to generate a similar ΔV.
In “A Minimal-Mathematics Introduction to the Fundamentals of Random Vibration & Shock Testing,” Wayne Tustin writes,
“We now know that none of those shapes occurs in the ‘real world‘…testing machines and procedures were long ago developed to generate those unidirectional, classical pulse shapes. They contain much more low-frequency energy than do most ‘real world‘ shock pulses. Often they are deficient at extremely high frequencies” (Tustin, pg. 335).
That being said, classical pulses have historical precedence and generate very well-known responses for product evaluation and durability testing. Many test standards define classical shock pulses, including MIL-STD-810, DO-160, ISTA, ASTM, SAE, and IEC 60068. An example of a classical shock test definition might look like the following: 3 – 10mS, 20Gpk, half-sine pulses in all six orthogonal axes for a total of 18 shocks.
While test specifications often define classical shock pulses, more advanced shock testing may require a complex transient pulse that cannot be replicated by a classical shock pulse.
Complex Shock
Some vibration specifications require a user-defined transient or shock response spectrum (SRS) for more complex shock pulses. There are specialized software packages designed to re-create these complex pulses.
Test engineers can use complex shock pulses to represent real-world conditions more accurately. Many synthetic, calculated pulses can simulate a complex transient waveform with a frequency response comparable to the field environment.
It is also possible to replicate a recorded signal from the field and process it using an iterative shock control loop to generate and control the complex waveform effectively.
Equipment and Software for Shock Testing
Classical shock testing is run on a mechanical shock machine, electrodynamic shaker, or servo-hydraulic shaker. The system selected to generate the shock pulses depends on the product’s mass, the desired amplitude in acceleration, velocity, or displacement, and the defined pulse shape. The following lessons discuss more on shock machines and shakers.
Accelerometers
Classical shock testing is run on a mechanical shock machine, electrodynamic shaker, or servo-hydraulic shaker. The system used to generate the shock pulses depends on the product’s mass, the desired amplitude in acceleration, velocity, or displacement, and the defined pulse shape. The following lessons discuss more on shock machines and shakers.
Accelerometers are typically used to measure shock tests, which convert mechanical motion into an electrical signal. Depending on the shock pulse’s characteristics, the engineer may need different accelerometers to measure the test results.
Specialized shock accelerometers are designed to measure extreme transitions in a shock test more accurately. While these aren’t necessary for every shock test, they are useful, especially for measuring high amplitude, short-duration pulses.
For example, piezoelectric accelerometers use a piezoelectric crystal to generate an electrical signal based on the compression of the crystal by some known mass. They are used as a reference, such as the control signal for shaker testing, and additional monitoring points to observe a product’s response to an impulse.
Software
Some software packages are designed to run specific testing such as IEEE-344 tests, chatter monitoring, and other advanced analyzer functions. These transient events are difficult to characterize and analyze. Test engineers commonly use additional analysis tools like waterfall plots, energy spectral density, coherence plots, and transfer function plots, depending on the environment and application.
Conclusion
Shock testing confirms a system’s ability to withstand a transient shock. Many test specs include shock testing with a defined shock pulse. There are two categories of shock pulses; classical pulses are simple and unipolar, but some tests require more complex pulses.