Sensor Specifications
June 10, 2022
Back to: Sensors for Vibration Testing
An engineer must select a transducer with test specifications in mind. Sensors contain a range of data, but some parameters are more relevant to vibration engineers than others.
Most specifically, vibration engineers must consider the test’s acceleration range. The transducer needs to measure peak acceleration values without becoming saturated.
Sensitivity
Sensitivity largely determines a transducer’s range of acceleration. This value describes the change in an electrical output in relation to a physical input signal.
Transducers arrive with a calibration certificate that includes their sensitivity. Calibrated sensitivity ratings are in millivolts (mV) over an engineering unit; the unit for accelerometers is typically mV/G.
The most common accelerometer sensitivities for vibration testing are 100mV/G and 10mV/G. The measurement range can be calculated from the sensor’s sensitivity and output signal.
For example, most integrated electronics piezoelectric (IEPE) accelerometers can output a ±5V excitation signal. The range of a 100mV/G accelerometer with a ±5V output is 50Gpk (5Vpk/100mV = 50Gpk), and a 10mV/G accelerometer is 500Gpk (5Vpk/10mV = 500Gpk).
These IEPE accelerometers can generate a signal greater than ±5V; however, the response will no longer be linear, and the overall measurement uncertainty will significantly increase.
Importance of Sensitivity
Accelerometer sensitivity is necessary to consider as structures often have high resonances measuring over 50G. A 100mV/G accelerometer is typically limited to 50G measurements, meaning measurements around 50G will be inaccurate and subject to clipping.
A 10mV/G accelerometer has lower voltage outputs for a given excitation. Low-acceleration signals may be lost in the controller’s noise floor. If the engineer uses a quality controller with a low input noise floor, 10mV/G will provide satisfactory results around 500G.
Avoid Entry Error with TEDS
An engineer must enter the correct sensitivity values when setting up a test. An incorrect value can cause significant damage to the shaker and provide unreliable data.
For example, suppose an accelerometer is calibrated to 10mV/G, but the test engineer mistakenly enters 100mV/G. If the accelerometer detects a 10mV value, it will display a 0.1G acceleration value rather than 1G. As a result, the data will be off by a factor of 10. The difference in this example is drastic, but even a slight deviation from the certified value can lead to error.
A transducer electronic data sheet (TEDS) is stored in the memory of an IEPE accelerometer. The TEDS chip contains the accelerometer’s calibration data and other information such as its calibrated sensitivity, calibration date, serial number, manufacturer, and calibrated frequency range. An engineer can import this information to the control software to avoid entry errors.
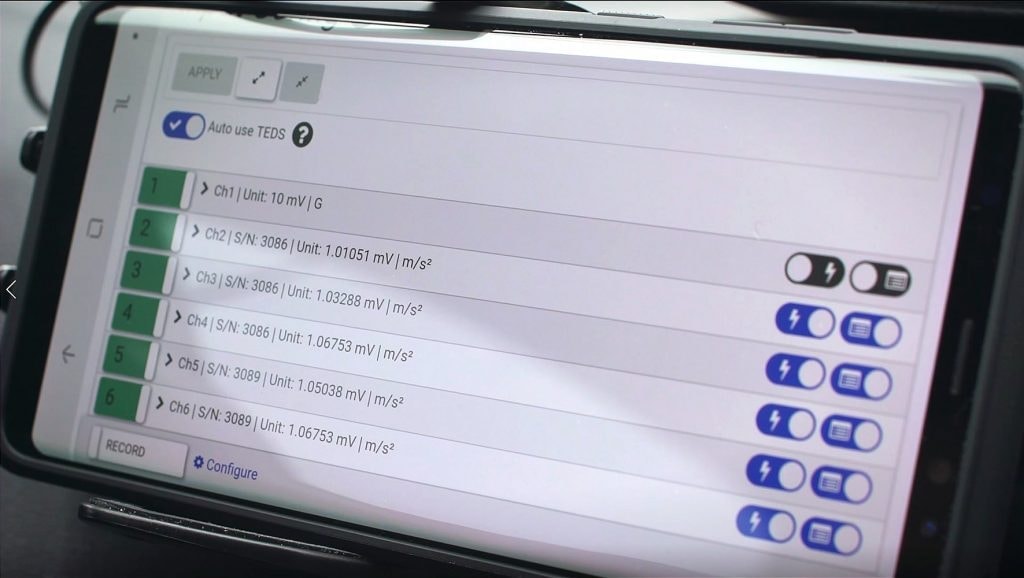
Auto use TEDS option in VR Mobile.
IEEE 1451 defines the standards for TEDS, which depend on the sensor type and data type.
Frequency Range
Transducers also have a frequency range with an upper limit set by the linearity of its sensitivity over the given range. It may include a tolerance defined as a percentage or decibel, such as ±5% or ±3dB.
A transducer’s sensitivity will increase as the frequency approaches its resonance. Selecting a transducer with the correct frequency range and mounting it properly will help ensure accurate results at high frequencies.
Additional Specifications
While sensitivity and frequency range are the primary specifications to consider for a vibration test sensor, there are many others. Their importance varies based on the test conditions. Additional specifications include internal capacitance, transverse sensitivity, and weight. Environmental conditions also play an important role in sensor selection.
Environmental Specifications
A sensor must be able to operate under a test’s range of environmental conditions, including extreme levels. For example, a sensor is unsuitable if it can function at the amplitude of interest but not at the maximum amplitude. If the test exceeds the sensor’s amplitude range, then signal distortion will occur.
Most commonly, engineers reference a sensor’s temperature range and humidity. However, there are other considerations for different test types. Other environmental conditions include:
- Pressure
- Acoustic level
- Nuclear radiation
- Electromagnetic fields
- Noise floor
- Grounding
- Corrosion
- Explosion-proof
- Strain
- Intrinsic safety
Calibration
Vibration test results depend on the accuracy of the equipment. Even with a quality controller and shaker system, a vibration test needs a transducer that properly controls and detects vibration. Consequently, the accelerometer must be accurately calibrated.
Calibration accurately determines an accelerometer’s sensitivity at various frequencies of interest. A calibration schedule helps labs detect incorrect sensor sensitivity and discover sensor defects to have confidence in their results.
For the best practices for accelerometer calibration, please visit the article Best Practices for Accelerometer Calibration.
Learn more: Calibrating a Piezoelectric Accelerometer in VibrationVIEW VRU course.