Electromagnetic Interference (EMI)
February 12, 2020
Back to: System Noise and Ground Loops
Electromagnetic interference (EMI) is the electromagnetic disturbance of one electrical device onto another. It is also called radio frequency interference (RFI) or RF noise.
EMI can derive from a communication system, such as a CB radio, but electronic devices are most often the culprit. The interfering device can be virtually anything, from an electric drill to a garage door opener to fluorescent light ballasts. Even electric power lines can cause EMI.
EMI can disrupt the operation of electrical equipment, reducing its performance or leading to malfunctions. Sometimes, it can corrupt data in communication systems, resulting in lost or distorted signals. Prolonged exposure to EMI can also degrade sensitive components, shortening their lifespan.
Vibration Testing
EMI can significantly affect the performance of a vibration testing system when electrical noise is in the surrounding environment. Long cables, poorly shielded cables and components, and certain amplifiers can act as antennae, pick up EMI, and introduce it into the test system.
EMI interference can distort vibration measurements, leading to inaccurate test results or inconsistent system behavior. Proper grounding techniques, cable management, and high-quality shielding are necessary to minimize EMI and maintain test reliability.
Detecting and Minimizing EMI
Vibration Control Systems
The simplest way to detect EMI in a vibration control system is to move the cabling. If the input’s signal shows variation when you move the cabling, then EMI is the most likely culprit. Monitoring signal integrity with an oscilloscope or spectrum analyzer can help identify the frequency and source of interference. Unusual spikes or patterns in the signal are indicators of EMI.
In a typical lab, electrical noise can be generated by fluorescent lights, electric motors, pulse width modulators, and many other systems. Most cables have shielding to protect the circuitry, but it can wear down over time. Regular inspections of cables for physical damage, wear, or corrosion help prevent EMI issues. Replacing aging cables and connectors with high-quality, shielded alternatives can reduce susceptibility to interference.
To minimize EMI, consider the following suggested practices:
- Proper grounding
- Separate high-power devices from sensitive systems
- Reroute cables to avoid parallel runs with power lines
- Eliminate unnecessary sources of electrical noise
Hardware Solution
If replacing the cables or moving the cables into a protected location away from high voltage wires, light, and other RF noise sources doesn’t resolve the issue, then connecting jumpers on the front panel of the VR9500 can minimize the effects of EMI on the system.
VR9500 Jumpers
The VR9500 vibration controller has jumpers on the front input panel to address EMI. In most cases, the jumpers are not connected when a VR9500 is shipped from the factory.
When connected, the jumpers mechanically bond the shield/ground side of the input channels directly to the ground reference (see the next lesson for a discussion of electrical ground.) This bond bypasses some of the protective circuitry which could act as an amplifier for EMI and convert it into a measurable voltage. By bypassing the circuitry, the jumpers reduce or eliminate the effects of EMI on the system.
For detailed instructions on connecting the VR9500 jumpers, ask the VR support team for the document “VR9500 Front Panel Bypass Jumpers,” or follow our noise troubleshooting tips under the Noise Troubleshooting section of this course.
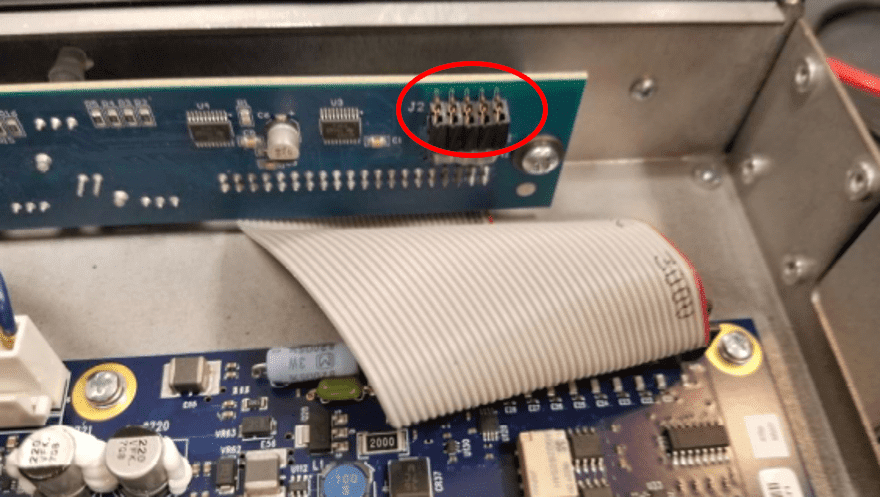
Figure 1.1. Unconnected jumpers on the VR9500 front input panel.
There are two downsides to connecting the VR9500 jumpers: (1) it bypasses the 200V transient peak protection circuitry built into the VR9500 and (2) differential mode cannot be used.