Understanding the Device Under Test
July 19, 2024
Back to: Making Sense of Test Data
A “good” vibration test profile, meaning one that is efficient and accurate, begins with the engineer’s knowledge of the device under test (DUT). Of course, the quality of data, processing, fixturing, and control play an imperative role in a test’s success, but understanding the DUT’s end-use environment and its behavior when in use helps engineers build an accurate test profile. When the test profile reflects the DUT’s application, the possibility of an unsuspected failure in the customer’s hands lessens.
Before testing, the engineer should collect information about the DUT and review it alongside their test objectives. In the product development cycle, this process occurs during the statement of requirements and proof of concept phases (Figure 1). It may include data acquisition in the end-use environment or gathering historical references on the same or similar devices. The amount of detail will depend on the project’s timeline, resources, and goals.

Figure 1. Example of a product development cycle.
Understanding the DUT
This lesson includes suggestions for gathering information about a DUT to build a good vibration test profile.
- Review product specifications, including safety, performance, and reliability requirements
- Analyze the DUT (design failure mode and effect analysis – DFMEA)
- Assess the end-use environment, accounting for all use cases in all markets
- Define a data acquisition, data processing, and testing plan
Review Product Specifications
In a typical product development cycle, the statement of requirements should identify all performance, safety, and reliability requirements for the DUT’s application. The engineer can use this information to define the pass/fail criteria for safety, performance, or other factors with appropriate detection and design controls.
Pass/Fail Criteria Examples
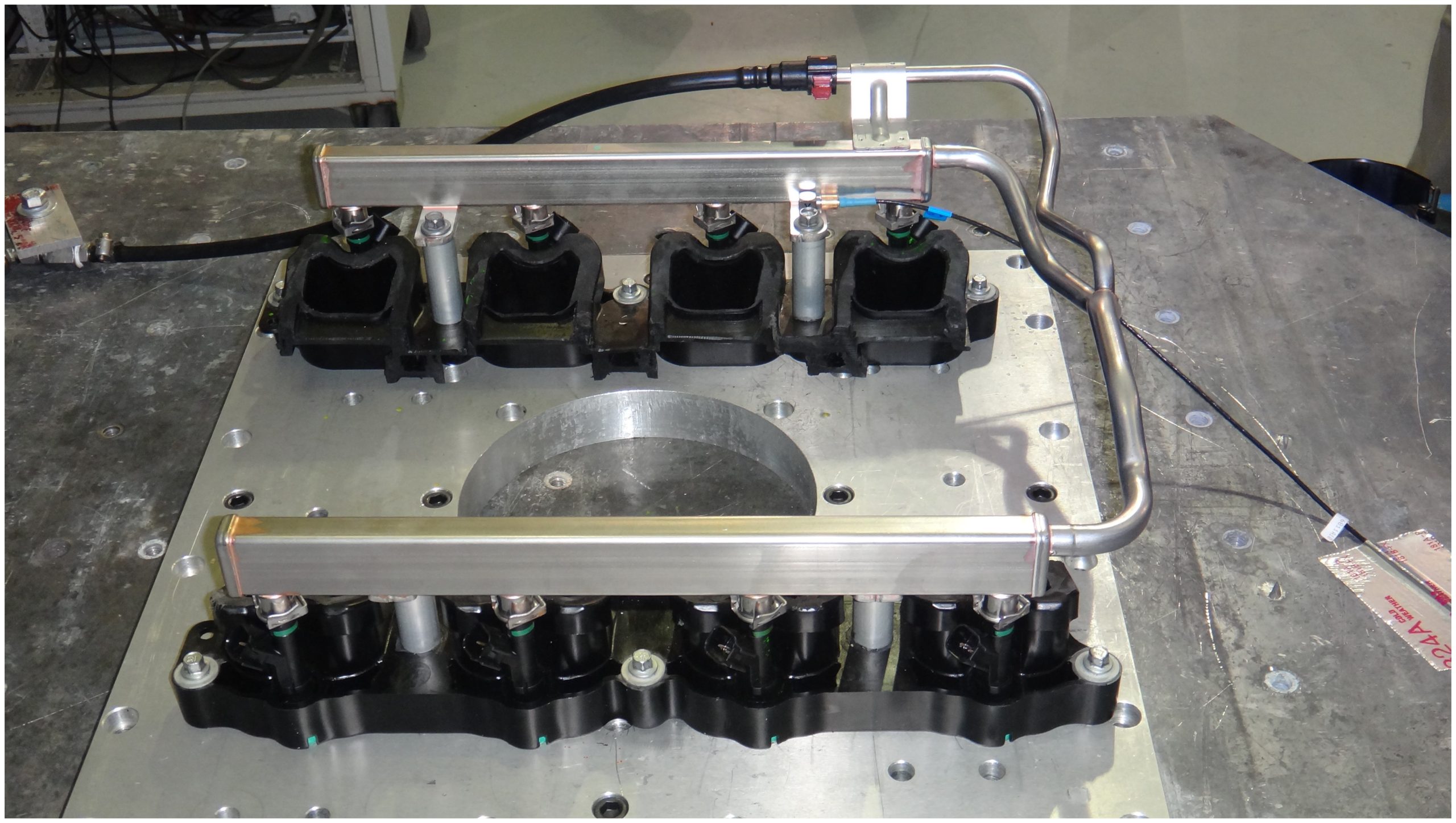
Test setup example for identifying failure modes.
- Resonance shift by 10%
- Solder crack
- Loss of pressure (seal leak)
- Intermittent electrical signals
- X amount of material degradation halfway through test, at end of test, etc. (ex. connectors and wiring harnesses)
- 10% loss of torque (ex. fasteners)
- Structural crack greater than 3 mm (ex. brackets)
When defining pass/fail criteria, the engineer should be able to answer two questions:
- What does the test mean if the parts pass?
- What does the test mean if one or more parts fail?
To understand this idea further, consider a test engineer’s four potential test results:
True Pass
Manufacturers and other organizations write test specifications as “success run” reliability demonstrations, so a test is useless if it misses failure modes. As such, high-fidelity data that correlates to the operational environment is essential. (Vibration test specifications are often written as “success run” so suppliers can predict cost and timing, although test-to-failure methodologies are more useful in many respects.)
True Fail
There is often significant organizational pushback when engineers identify test failures. With irrefutable recorded data to correlate the operational environment and established test acceleration methodologies, an engineer should have no problem convincing an organization that a design change is necessary to avert future issues.
False Pass
A false pass is never good but occurs regularly. It leads to product recalls, warranty costs, liability, and harm to reputation. Fortunately, they are less common when a test has quality specifications from the start, including good field data and sound methods for test development.
When a false pass does occur, field data applied competently to test development can:
- Provide a defense for the manufacturer and reduce damages awarded to plaintiffs
- Reveal the deficiencies of the original test, approve the revised design, and resolve the recall issue
False Fail
A false failure leads to scrapping or reworking costly prototypes, resulting in loss of time, unnecessary investigations and design changes, and additional testing costs. It occurs often and is obvious when the engineer gathers data at the outset of product development and processes it into a field-correlated accelerated test.
Analyze the DUT and End-use Environment
Engineers can begin to build a good vibration test profile by 1) assessing the DUT’s end-use environment (EUE) and 2) defining issues/limitations with the DUT’s initial design.
Assess the EUE
A DUT’s EUE involves the physical environment and any individual components’ exposure to external forces within the design. Data can include vibration, mechanical shock, thermal, electrical, corrosion, humidity, cyclic loading, etc. The engineer should ask:
- What ordinary loads will the DUT potentially experience during everyday use?
- What extraordinary loads might it have to survive?
Engineers can record these data in the lab/field, reference historical data, or use industry standards. They should also consider how these environmental factors interact (e.g., vibration frequency shift due to thermal changes).
Define the Initial Design
Design failure mode and effect analysis (DFMEA) is a procedure that identifies a DUT’s failure modes/mechanisms throughout the development cycle. In the proof-of-concept phase, a DFMEA should include tests that root out obvious design flaws and confirm the upper and lower environmental operational points and design destruct limits. The next lesson describes these tests in more detail.
Engineers should perform these tests early and with relatively few DUTs. They should repeat the tests as they identify failures and evaluate proposed solutions. Engineers can also use this time to test system elements, such as a circuit card or cooling loop seal design.
Define a Test Data Acquisition Plan
After the engineer has set pass/fail limits and assessed the DUT and environment, they must define the test setup. Given the DUT’s behavior, they establish accelerometer mounting locations, test settings (sampling rate, filtering, etc.), durability schedules, and conditions (speed, gear, acceleration rate, etc.).