Force and Pressure Sensors
June 10, 2022
Back to: Sensors for Vibration Testing
In addition to vibration, products respond to other physical events in the operational environment. Measuring force and pressure is common in manufacturing to test the product against dynamic force, impact, or compression.
Force Sensors
Force sensors measure the interaction between bodies, whether it is tension, compression, or shear.
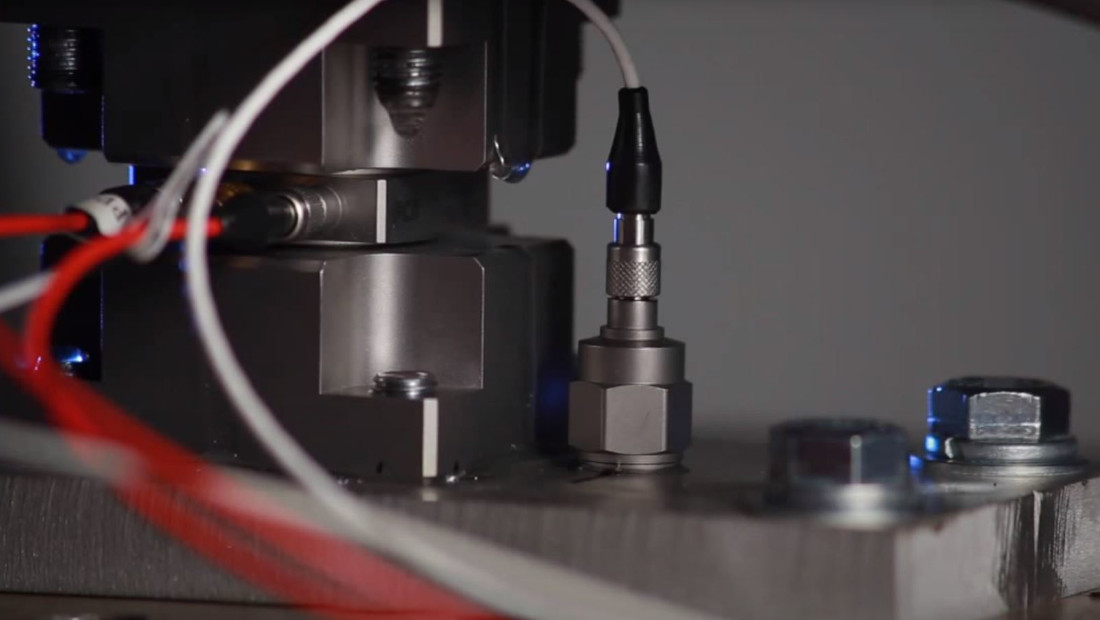
Force transducer mounted to a shaker head.
Many technologies measure force, but, most often, force sensors implement a piezoelectric quartz or strain gauge.
For example, a load cell converts force to an electrical signal to measure a compression value such as weight. Load cells can use a piezoelectric crystal, a strain gauge, or another technology type.
Pressure Sensors
Pressure describes the force applied to a unit of area due to the change in linear momentum of gas or liquid molecules. Pressure is static: a scalar quantity not dependent on direction. However, when its measurement depends on the direction of motion, pressure is dynamic. Events such as turbulence, engine combustion, and ballistics call for dynamic pressure measurement.
Pressure sensors convert pressure to an electrical signal to measure pressure, force, or airflow. There is various pressure sensing technology, although piezoresistive sensors are predominant because they can change their electrical resistance proportional to strain.
A pressure sensor may be categorized by the pressure type it measures, such as gauge or differential, or the technology it employs. When selecting a pressure sensor, technicians should consider the system’s maximum pressure, the test environment, and accuracy requirements.
Strain Gauges
A strain gauge (or strain gage) is a sensing device that measures the piezoresistive effect: a change in a material’s resistance due to strain. Many transducer types include a strain gauge, including pressure, load, and torque measurement devices.
Other types of strain gages can be attached directly to the device under test. Often, the sensing element is a metallic foil in a grid pattern bonded to the carrier. An excitation voltage is applied across the bridge, and the strain gauge measures the change in electrical resistance of the sensing elements.
The Wheatstone bridge is the basis for most bonded strain gauge configurations. It is a circuit with four resistive legs, each of which can be an active sensing element. The number of active strain sensing elements—one, two, or four—determines the circuit’s configuration. The position of the sensing elements and the measurement type also characterize the bridge configuration.
Alternative types of strain gauges include capacitive strain gauges, piezo-resistors, and quartz crystal strain gauges.
Microphones
Sound is a mechanical wave produced by a vibrating object. As a sound wave travels, it forces a change in atmospheric pressure. A microphone can measure this change in pressure and output an electric analog signal for analysis.
Engineers measure sound pressure in various frequency ranges; the audible frequency range captures the human auditory field of 20 to 20,000 hertz (Hz). The human ear responds to frequency measurements on a logarithmic scale, so the frequency content of acoustic signals is often processed into proportional frequency bands called octaves.
Sound pressure levels (SPL) are a measurement unit comparable to human response. It is a ratio of the sound pressure to a reference sound level; the most common reference is 20μPa.
SPL measures the alterations in pressure due to a sound wave that has traveled some distance. In comparison, sound power level measures a source’s emission of sound waves and is not affected by distance. As a power measurement, the sound power level uses the SI unit watts. Like sound pressure, it is often expressed in decibels (dB).
A product test engineer may want to measure SPL for safety and customer satisfaction. For example, a vehicle with a quiet ride is preferable for most consumers.
Alternatively, an engineer may want to measure a test item’s response to sound pressure for structural qualification. For instance, the acoustic environment of a rocket launch is significant enough to influence some spacecraft components.
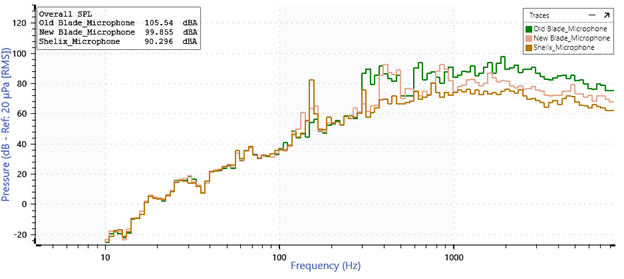
Comparison of sound pressure levels.
Externally Polarized and Pre-polarized
Similar to ICP/IEPE accelerometers, microphones can have an internal power source on the backplate to measure the change in capacitance. Externally polarized microphones use a separate 200V power source and require an external preamplifier. Pre-polarized (0V) microphones have a 200V power source on the backplate, which allows the device to use a constant current supply/signal conditioner as a power source.
Externally polarized microphones perform better at higher temperatures and offer a higher output voltage, but pre-polarized microphones have a more streamlined setup.
Specifications
There are several types of measurement microphones and more precise condenser microphones. Their primary function is to electrically reproduce a sound wave without distortion.
Microphone sensitivity describes the relationship between the output voltage and input sound pressure. A microphone’s sensitivity needs to be constant over the frequency and temperature range to avoid distortion to the output signal. The dynamic range, total harmonic distortion, and frequency range are other specifications to review when selecting a microphone for testing.